

Mining in Monroe
By Jim Rogers
Before 1700 most of the iron used by the colonists came from across the Atlantic, mostly from Britain. Its cost was high because of a shortage of wood for charcoal and also high shipping cost.
In 1736, Cornelius Board, whose descendents still live in Monroe, was actually looking for gold and silver when he found outcroppings of iron ore. He explored up the Ringwood River to the foot of Sterling Lake. He purchased two tracts of land that included Sterling Lake and started manufacturing iron, probably the first ironworks in the state of New York.

Here in the Ramapos (Indian for Land of Slanting Rock) was part of the answer to the high cost of imported iron. The iron deposits here were what geologists call magnetite, a form of iron oxide with the highest known content of iron. It could be mined easily; it could be smelted by familiar techniques and unlimited quantities of wood were available to make charcoal fuel. These were the ingredients for profitable iron making. The Ramapos also provided swift streams that would provide waterpower for bellows, tripping hammers, and sawmills. Last but not least, lime was available for fluxing the blast.
Another important fact was that the iron found in the Ramapo Mountains was close to the Hudson River for transport. Monroe’s boundaries extended to Stony Point on the Hudson River in those days.
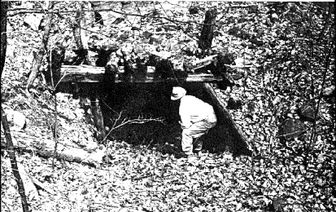
The colonies by 1720 were exporting ore to Europe. This could be done cheaply as ballast was needed for ships making the return trip. Exports to England alone in 1770 was 8,000 tons. By 1775 production of iron and ore had increased to 15% of the worlds supply, which was more than England and Wales combined.
The mines themselves were of three general types: open pit, with the ore near the surface and easily accessible; the slope, a slanting tunnel which would follow a vein of ore as far as practical; and the pit type which was a perpendicular shaft to various depths with tunnels following the vein away from the shaft.
The fuel that the iron makers relied on for the early furnaces was charcoal. Wood was plentiful and gangs of woodcutters would cut down huge amounts of trees in the winter after the sap had retreated to their roots. Wood cut in the winter is harder and dries faster and when charred produces a superior charcoal. After they were cut to the proper lengths, they were hauled to the burning area which was level and sheltered. They were then stacked in conical piles and covered with sod, moss, and wet leaves. This blanketed cone was set on fire by dropping lighted chips down a small flue or hole left when stacking and covering the pile. These firings called for a lot of experience.
The fuel that the iron makers relied on for the early furnaces was charcoal. Wood was plentiful and gangs of woodcutters would cut down huge amounts of trees in the winter after the sap had retreated to their roots. Wood cut in the winter is harder and dries faster and when charred produces a superior charcoal. After they were cut to the proper lengths, they were hauled to the burning area which was level and sheltered. They were then stacked in conical piles and covered with sod, moss, and wet leaves. This blanketed cone was set on fire by dropping lighted chips down a small flue or hole left when stacking and covering the pile. These firings called for a lot of experience.
